75,715 sq. ft.
Lake Forest, CA
Pacific, an Oldcastle® copmany
Matthew Merritt, PE
Red One Engineering
Geogrid Retaining Wall Systems, Inc
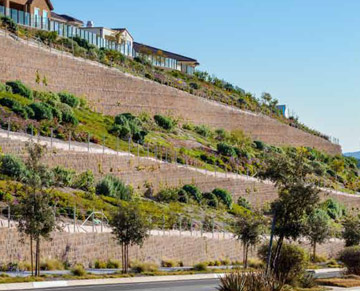
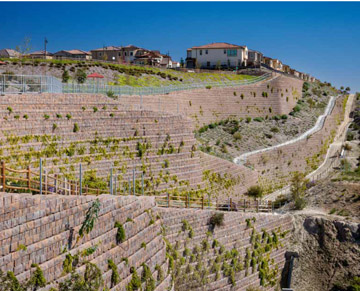
75,715 sq. ft.
Lake Forest, CA
Pacific, an Oldcastle® copmany
Matthew Merritt, PE
Red One Engineering
Geogrid Retaining Wall Systems, Inc
Developing Portola Hills required converting the site from its natural state of valleys and steep hillsides into acres of construction-ready flat pads. Among the challenges were that it was in a seismic area and had poor soil quality, with failure planes throughout. A failure plane is a weak clay layer that causes instability. These thin layers are like grease which, once exposed, cause landslides as dirt and rock slip over them. This is especially the case when there is significant rainfall, as there was throughout the fall and winter of 2015/2016. There were also design requirements the team had to meet for the project, including the city’s demand that most of the walls be plantable.
An expansive segmental retaining wall system was needed to create the buildable space. Baldwin & Sons chose to work with Geogrid Retaining Wall Systems, Inc., the largest segmental retaining wall installer in Southern California. “There’s not much flat land left in Southern California, and there is a shortage of homes in Orange County, so installation of a retaining wall system is an investment in creating more property square footage to build homes on,” said Geogrid owner Mike Stevenson.
The project was broken into three phases: Portola Northwest, Portola Northeast and Portola South. A variety of Diamond® Pro blocks as well as Vertica Virtual Joint (VJ) and Planter blocks were chosen to make up the wall system.
Geogrid’s in-house design engineer, Matthew Merritt, PE, of Red One Engineering, designed walls comprising the entire perimeter of the project to develop “super pads,” acres of flat land for Baldwin to build on. Many of these walls reached up to 49 feet tall and 1,000 feet long.
“We worked with the geotechnical engineer on the global stability analysis and incorporating Mirafi global stability geogrids into the wall design. Portola South had a long (100’+) and very strong geogrid for global stability. Portola NE had two walls incorporated into a large landslide buttress,” said Merritt. “We also worked with a shoring contractor to incorporate the Diamond Pro block facing over the shoring elements.”
To address global stability in the seismic areas, the team designed a system of secondary geogrids, placed between the standard grid layers. A grid’s length is usually equal to 100 percent of wall height. At the Portola site, between every layer of standard-length grid and compacted fill was another, smaller grid of only four feet long. These strata provided the necessary additional stability in the seismic area.
Geogrid’s choice of ANCHOR DIAMOND℠ plantable blocks gave Baldwin & Sons the maximum amount of space on which to build homes. This is because ANCHOR DIAMOND’S Plantable system has an 8:1 batter and the competitor’s block has a 4:1 batter.
“The wall batter is a ratio of vertical feet to horizontal feet, so 8:1 means for every eight feet vertical the wall slants backwards one foot so one foot of useable property is lost to the wall batter. The competition at 4:1 loses one foot every four feet of height, or two feet for every eight of height,” explained Merritt. “Using the various ANCHOR DIAMOND products provided the client with an additional 66,500 SF (1.5 acres) of usable land compared to using the competition at 4:1 batter.”
“The fact that Belgard offers so many complementary products that we could use both as vertical and plantable walls was a huge asset. The manufacturing of the product was also outstanding. We were installing more than 1,000 square feet of block a day, and they were always timely with manufacturing and delivery,” said Mike Stevenson, Owner, Geogrid Retaining Wall Systems, Inc
The last portion of the project, Portola Northeast, is scheduled to be finished in December 2023. “We used the full line of ANCHOR DIAMOND products available to us to meet the needs of the owner and requirements of the City of Lake Forest. The result was great looking plantable and nonplantable walls that blend into the site, provide an excellent aesthetic and most importantly provide lasting confidence in their structural capabilities,” said Merritt.